A time-honed, seed development process.
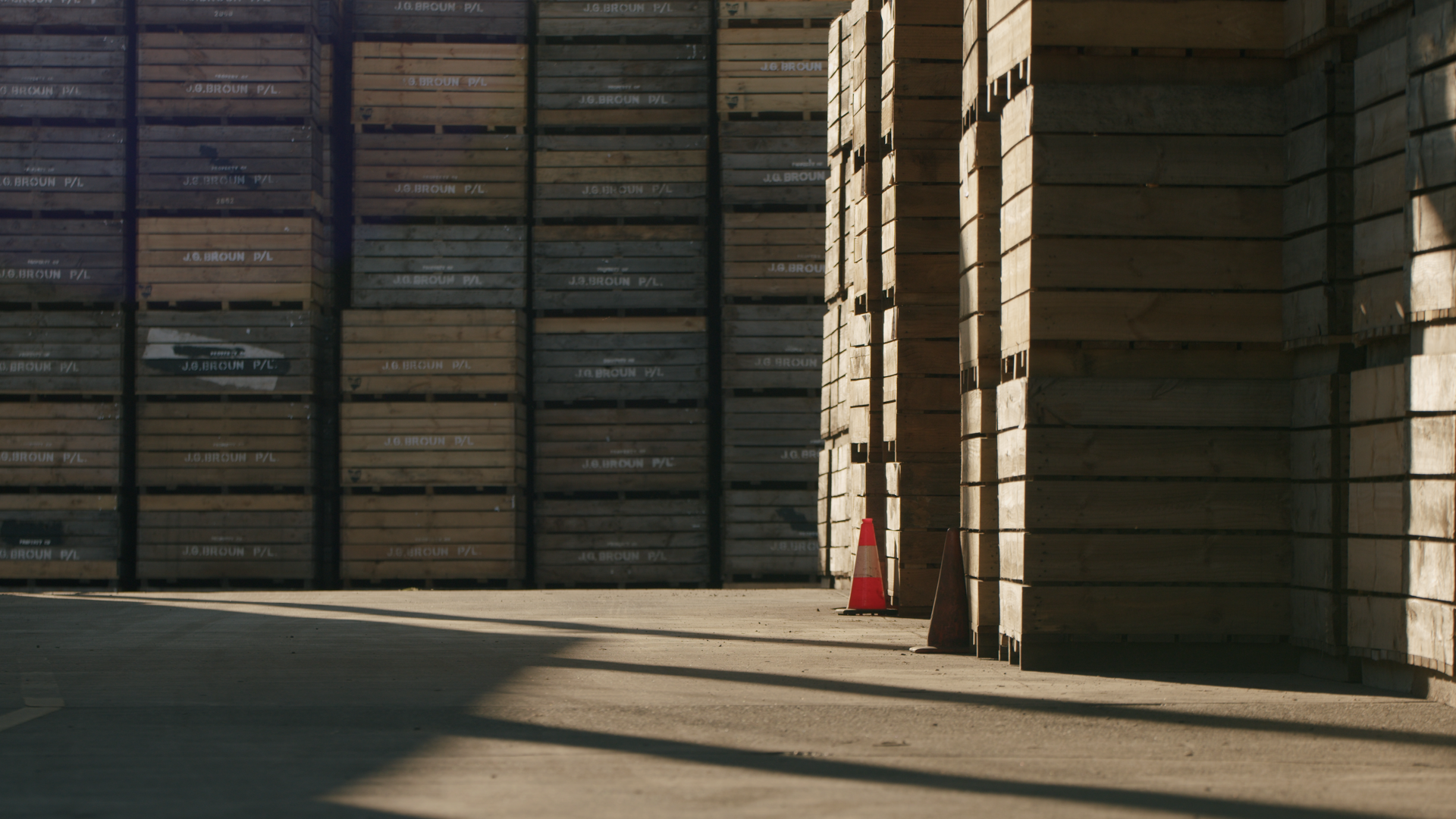
Sterile environment aids in ensuring maximum yield
Keeping disease and infections to a minimum is vital to the quality of the seed produced and directly affects the quality and quantity of the yields in following generations. For example 1 tonne of quality seed has the potential to produce a yield ranging from 15-30 tonne of the following generation of seed. Fungicides are added to the potato seed at intake (if desired), to minimise infection and optimise seed quality.
Cleanliness is paramount, with all processing equipment being sterilised after each line/crop is processed. JG Broun prides itself on maintaining a clean and sterile environment at all times. An accurate customer tracking and labelling system ensures all potatoes are traceable, which allows an accurate storage process, and customer demand to be managed efficiently and in a timely manner.
Learn More about our process.
-
Once harvest is complete, the potato intake arrives for grading in March/April and continues through to Mid June.
Most seed is then graded, certified and placed in cool storage. Some customers choose to download the seed directly into bins, allowing them to heal, before finally placing them into cool storage.
There are up to five generations of seed which include:
- Gen 1 and 2 (most valuable)
- Gen 3 (mother seed)
- Gen 4 (seed + commercial)
- Gen 5 (commercial)The certification process of grading is overseen by the Tasmanian Institute of Agriculture.
-
We offer a wide range of cool and dry storage options for our clients.
Potatoes are stored between March-November in a cool, dark, clean environment. The temperature ranges from 2-3 degrees and is closely monitored to minimise moisture loss and CO² levels.
During cool storage the storage rooms are vented for a pre-determined period of time, to manage and maintain the level of carbon dioxide (CO²) and oxygen (O²) in the cool storage rooms.
-
As Spring approaches, the potatoes are moved from cool storage to dry storage to warm up, ready for cutting.
The seed needs to be warmed at above 10 degrees (for approximately 10 days) prior to cutting. The seed is then cut, fungicide applied (if required), then the potatoes are allowed time to heal any wounds prior to planting, to minimise infection.
Our machinery has a number of sterilisation units positioned throughout the workflow process and the grading and cutting room is thoroughly cleaned before individual client’s batch is processed.
Some seed potatoes of the correct size (so called rounds) do not require cutting.
Our cutting process is of the highest quality and mostly automated, however past this point , hand cutting services are engaged to ensure premium seed output.